Doka to form in a double star system
Doka to form in a double star system
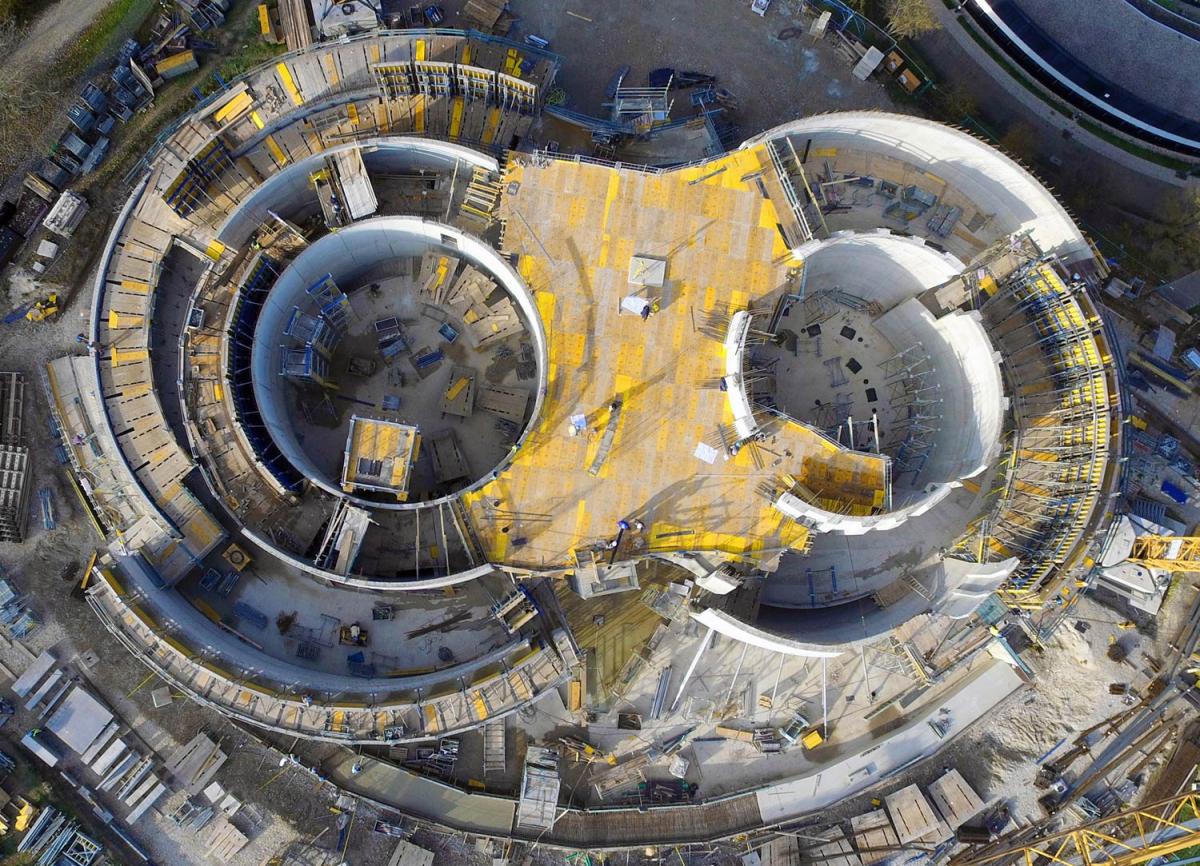
A one-of-a-kind cast-in-place structure is currently under way near Munich: the ESO Supernova Planetarium and Visitors Centre.
The building's cubature takes its cue from a narrow double star system. The architecture of the construction project is characterised by inclinations up to 23 degrees and demands the ultimate in artful engineering from contractor and formwork supplier.
The city of Garching located 15 km north of Munich is the headquarters of the European Southern Observatory, the European Organisation for Astronomical Research in the Southern Hemisphere (ESO). This is where a new planetarium and visitors centre reminiscent of a narrow double star system is under construction. In this concept, one star transfers its mass to the other. As a result, the heavier star explodes in the form of a Supernova. It briefly shines as brightly as all the lights of the entire milky way's stars together.
The spectacular design was conceived by Darmstadt architects Bernhardt + Partner. GROSSMANN Bau & Co. KG of Rosenheim are in charge of construction. They rely on cooperating with Doka Formwork Experts from their nearby Munich branch.
Unique architecture
The formwork has to fit perfectly from the start. The convex and concave walls present significant challenges for the formwork. In the lower cycles the cast-in-place building construction sections open up towards the top before the walls start sloping toward each other again. Each pouring cycle is different. Each formwork panel is unique. It fits only in a single spot in the structure.
On top of it, everything has to be delivered and made available on-time and then returned. For this purpose, Doka's Formwork Experts developed an efficient concept that includes 3D planning, panel assembly and disassembly and logistics.
Strong wall formwork
Element grilles of the Large-area formwork Top 100 tec are put to use here. Their heavy-duty components, WU14 waling and I tec 20 beams, allow more freedom when placing type 20 anchors. In this combination the formwork accepts maximum concrete pressures with the least deformation.
These are ideal conditions for precisely fabricating the walls, some of which are 18 m high and inclined up to 23.5° and, in terms of layout, reminiscent of a lying number eight. Fine adjustments are accomplished by using top-mounted forming boxes. They are covered with an 8-mm Plex sheet and carefully screwed to an open formwork unit.
Precise panel assembly
Special factors or structural requirements and unique shapes call for customized solutions. Thus, all of the assembly work for these highly sophisticated formwork panels is completed at Doka's Pre-assembly Service in Maisach. These complex wall formwork panels are produced with maximum precision west of Munich and only 38 km from the construction site.
Assembly and delivery are matched exactly to the construction process and handled just-in-time and just-in-sequence. After only a single pouring operation the panels are returned to the Doka branch. There they are re-sized to fit the subsequent use cycle. The Doka Team will have assembled more than 7,800 m² of complicated Large-area formwork Top 100 tec.
Precisely aligned
However, the right formwork panels are only the first step in the process. Correct placement in the building is just as important. Contrary to common structures with their right angles, alignment is another major challenge here. This is the reason each individual formwork panel is aligned by means of a tachymeter. This step is supported by measuring points built into the form-ply. For its part, the tachymeter takes its alignment from a grid of coordinates specified for the entire site. To ensure proper placement, it is checked by two independent participants prior to pouring.
Shoring capable of supporting the load
In the rising cycles, the inclined wall formwork units are firmly and securely supported by a shoring structure consisting of the Load-bearing tower Staxo 100. Doka's Pre-assembly Service installed a 3-m wide platform level to serve as a superstructure. It allows the site crew to move without restrictions. It also provides the formwork with force-fitted support and secures it against wind exposure. Safety is ensured from the very beginning with protection screens from the Edge protection system XP attached to the outside.
Reliable cooperation
Elias Laar, Managing Director at Grossmann Bau is inspired by the partner-like cooperation with Doka Formwork Experts: "It simply works like a well-oiled machine. The performance is exemplary and the people backing up the brand are reliable. We are living partner-like cooperation on equal footing."
Construction for this extravagant building began in February 2015. Ever since, operations proceeded swiftly. The facility is scheduled to open in mid-2017. By that time, we will have produced a gross volume of more than 30,000 m³ at a level of maximum difficulty.