Formwork in every shape and dimension – even faster with the new CNC system
Formwork in every shape and dimension – even faster with the new CNC system
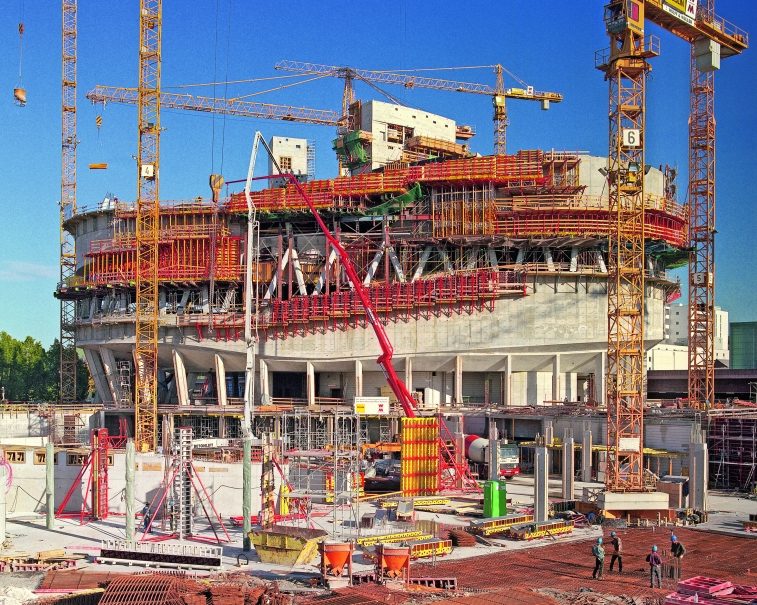
Planned, formed, concreted – it is actually hard to believe that this procedure could ever function trouble-free in some cases of present-day abstract concrete structures. In its pursuit of uniqueness, architecture is becoming more and more ambitious. Parallel to this, the requirements of construction companies are likewise increasing. PERI, however, is keeping pace with this trend: with individual formwork solutions, the formwork and scaffold expert ensures that complicated designs become reality. In order to increase the required capacity at the Weissenhorn formwork assembly plant, a second state-of-the-art CNC timber processing facility started operations in the spring of 2014.
In Mississauga, Canada, a pair of twisted high-rise buildings called Absolute World wind their way steadily upwards. Visitors to the Mercedes-Benz Museum in Stuttgart pass through two interlocking spirals which have designed to represent human DNA. In London, the undulating roof of the Aquatics Centre is visible from afar and whose movement is continued on the inside of the structure. And with the MONA office and commercial building currently under construction in Munich, the focus is on realizing in particular the beautiful flowing form of the parapets on inside the shopping centre
All these structures are not only the work of architects. In order to convert such visions into reality, the teamwork of various experts is required. Thus, as a specialist in the field of formwork and scaffolding technology, PERI helped in the realisation of these buildings by MAD Studio and Burka Varacalli Architects (Absolute World), UNStudio (Mercedes-Benz Museum) and Zaha Hadid (Aquatics Centre). As it happens, concrete is a flexible material and is particularly well suited for implementing complex building geometries. However, the more demanding the architectural design is, the faster formwork systems reach their limits. As a result, customized equipment has to be used more and more frequently. And in order to keep within the given budget and to finish on schedule according to the contract, contractors use the services of competent suppliers. In this area, PERI has been a very reliable partner for many years now.
PERI special formwork
PERI experts support the construction companies with an extensive range of services: from 3D planning and assembly of complex formwork units through to punctual deliveries and transparent billing.
On the basis of a 3D model, PERI engineers succeed in precisely tailoring project-specific formwork units of almost any shape in order to realise the ideas of the architect. Even before completion, planners can envisage the formwork solution for themselves with photo-realistic, moving and three-dimensional images. Moreover, the required on-site formwork assembly steps can also be visualized by animating the construction process. This ensures cost transparency and reliable calculations.
For every planning task, the engineers use as many system components as possible and therefore always find the most cost-effective way. Some projects can be realized by means of system formwork with individual special elements such as customized loose sheets, recess units in the floor, wall and ceiling or box-outs. For the construction of buildings that continually incline or have a curved design, however, unique special formwork is required. These are usually comprised of three-dimensional units and VARIO basic elements which are statically supporting.
In order to accelerate the production of the cut-to-size sheets and required formwork units, the company has invested in a second CNC timber processing facility at the Weissenhorn formwork assembly plant. The customized sheeting can now be produced using two sets of equipment in parallel. In particular, through the automated cleaning process and integrated feeding system of the new installation, the team can produce high volumes with millimetre-precision in the shortest possible time.
One of the big challenges of complex building geometries that very frequently has to be faced is ensuring the precise arrangement of the joint and tie configuration that is subsequently visible on the concrete surface. Other important factors for facilitating trouble-free on-site operations are also incorporated into the planning process; for example, very high fresh concrete loads which frequently occur in these projects or the site-specific boundary conditions during assembly.
The formwork sets are delivered punctually on the agreed date to the construction site ready-to-use and in the required quantity. PERI assembly and logistics staff coordinate capacity at the company´s own formwork assembly facility on an on-going basis. This means that customers can also have large amounts of materials at very short notice.
Due to the fact that these experts accurately cut-to-size and pre-assemble the 3D boxed elements in advance, the special formwork elements can then just as easily be put together as the standard systems on the construction site. On request, supervisors are available to provide professional briefings for the on-site assembly operations. As soon as the ideas have been "cast in concrete", the site management can also agree on a fixed price for the dismantling. Fact is, a large part of the individual components can be re-used for new projects.
All in all, the services also contribute to ensuring smooth and efficient construction even with difficult project requirements, and thus actively participate in the realization of today´s architectural highlights.