How to pull 1,000 tonnes fuel-efficiently
How to pull 1,000 tonnes fuel-efficiently
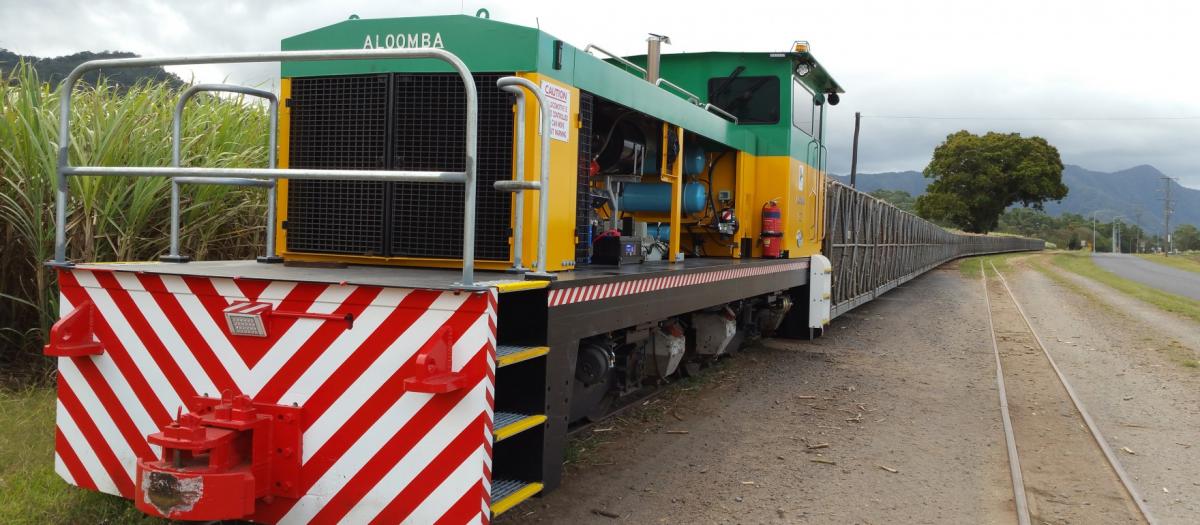
If you think pulling 130 tonnes is a tough test, have a look at this Scania V8-powered cane locomotive.
Mulgrave Mill, just outside Cairns in Far North Queensland, has installed a Scania 16-litre V8 in a refurbished sugar cane locomotive. The 588 hp Scania V8 has been hard at work for several months pulling 1,000-tonnes gross without even breaking a sweat. Even more impressive is the new engine’s fuel efficiency, almost twice that of the engine it replaced. It now consumes only 15.5 litres per hour, instead of the old engine’s 27 litres per hour, providing the operator with a meaningful reduction in operating cost.
Trusted engine supplier
This is the 3rd Mulgrave Mill locomotive to be repowered with a Scania engine supplied by Scania’s independent authorised dealer, RSC Diesels, based in Cairns. There are two further engine-repowering jobs in progress. The 50-year-old train, repowered with the Scania V8, was stripped to its chassis and received an all-new cab constructed in the Mill’s engineering workshop.
Keeping the fuel-efficiency promise
Ross Nucifora in the Meerawa locomotive.Ross Nucifora in the Meerawa locomotive. The V8 engine produces enough torque to haul a selection of 4-, 6-, and 10-tonne individual cane-filled carriages that add up to 1,000-tonnes gross. This is over a distance of 40-50 km, depending on the collection location, from farmer’s field directly to the sugar mill.
“It has been a good harvest this year so the V8 powered locomotive has been busy,” says Morty Owens, Mulgrave Mill’s plant engineer. “It is using around 15.5-litres of fuel per hour, which is what we expected. The other, 5-cylinder, Scania engines we have had in use for a couple of years have proven themselves. They have done what Scania said they would on fuel, between 12 and 14 litres per hour, pulling around 500-tonnes.
“We run each locomotive around 2,000 hours per season,” Morty says. “The engine that the V8 replaced had clocked up around 40,000 hours.” “RSC Diesels’ Ross Nucifora has looked after us well,” he adds.
Transmission adapted to high-speed engines
As with previous repowering jobs, RSC Diesels has replaced the original transmission with a bigger, heavier-duty, more cost-effective Allison unit that works well with a high-speed diesel engine for greater efficiency. “We put a lot of effort into designing a powertrain package that would work well in this 42-tonne DH-class loco,” Ross Nucifora says. “That included a control package similar to those fitted to the earlier repowers of ComEng locomotives.
“Each application has been different, so we needed to work out exactly how much horsepower was required, and how to achieve the best fuel economy. This is the first V8 repowering job we have done, and there is potential to repower further existing V8-engined locos found across the region in the cane industry,” Ross says.