ESI releases PAM-STAMP 2015
ESI releases PAM-STAMP 2015
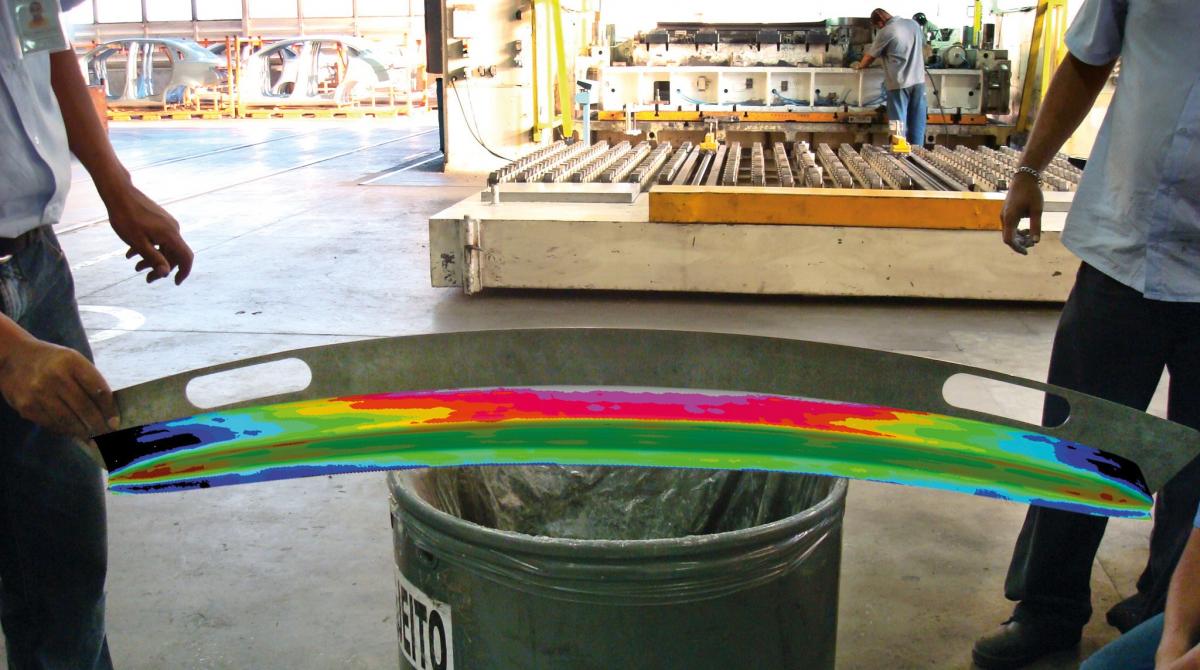
ESI Group, pioneer and world-leading solution provider in Virtual Prototyping for manufacturing industries, announces the latest version of its sheet metal forming simulation and die face design solution, PAM-STAMP 2015.
Addressing the needs of OEMs and tier-suppliers in the automotive, aerospace and heavy industries, PAM-STAMP precisely predicts the outcome of complete sheet metal forming processes. For manufactures this means saved time and cost throughout the entire product development cycle — from conceptual design to try-out and production. For tooling suppliers, PAM-STAMP uniquely enables production die engineering by providing high quality, predictive simulation to support styling of outer panels and also the development of new lightweight structural parts.
"Car manufacturers aim to shorten their development cycles, sometimes to under a year. As a result, it is essential to forming operation and tool design engineers to be assured of very high surface quality early in the tool development cycle." - explains Harald Porzner, Director of Virtual Manufacturing Product Management at ESI Group.
"Demand for accurate and defect free outer panels - especially with exciting stylings - has increased dramatically. Meeting that demand is even more challenging when using advanced material forming processes for structural parts. Reliable results in both cases depend on defining the tool geometry with great accuracy."
With these challenges in mind ESI delivers, with PAM-STAMP 2015, enhanced topology checking and geometry clean up and repair to enable most efficient geometry based die face design. Furthermore, with Die Starter, a brand new technology to generate the die surfaces needed to create a part, it is possible in the styling and design phase to generate fully automatically the die tools and to validate the forming results. The same technology can also be used in the concept development phase to generate automatically a starting point for refined die face design; saving a lot of iterations.
By accurately accounting for all aspects of the stamping process PAM-STAMP enables full feasibility assessment early in the process. It supports tooling and design engineers from concept through selection of tooling methods to try-out and final production; predicting the outcome of every step in the manufacturing chain before making any real prototypes. PAM-STAMP’s results can be easily transported to ESI Virtual Performance Solution so that product performance models properly reflect the “as manufactured” components.
ESI PAM-STAMP comprehensively addresses splits, wrinkles, springback and cosmetic defects like shock and skid lines, ski lines, and sinks. Defects are a critical concern for both exterior parts and structural components; in one case negatively impacting the visual appearance, and hence the consumer’s perception of the product quality, and in the second case potentially compromising formability to the shape required to achieve light-weight and performance.
"Vesta uses PAM-STAMP constantly for several stamped parts and processes. Our main objective today is to prevent and solve aesthetical defects and to develop springback compensation strategies for various parts throughout the entire manufacturing cycle." - says Arlem Picinin Campos, Manager of Simulations and Machining at Vesta Engenharia, Brazil.
With all the new developments it is now possible to manage cosmetic defects very early in the process and the structural performance at the right time, when designs are done.
With its particular capability to accurately simulate local bending and changing material properties, ESI PAM-STAMP 2015 provides even more accurate results. Developed over more than 25 years, in close collaboration with industrial and academic partners, PAM-STAMP addresses all types of sheet metal forming processes, including cold, warm and hot, and diverse metallic materials, including aluminum, titanium, and magnesium alloys, and different steels. Furthermore, the latest version of ESI PAM-STAMP adds a novel algorithm, based on an explicit computation strategy that delivers results three times faster than in the past. Coupled with the software’s capacity of directly using die surface designs from any CAD/CAE tool to simulation, engineers can realize time-savings of up to 90% as compared to traditional model set-up.
Accurate material information is crucial to successful simulations of sheet metal forming processes – which should be completed as early as possible in the development cycle. Addressing that issue, PAM-STAMP 2015 includes a new material database provided by an important partner of ESI; the Center of Precision Forming, at Ohio State University. In addition a new material law for hot forming (a unique strain path model) improves the precision of prediction of the geometry of the manufactured part; helping manufacturers better meet set tolerances.
Heat generated as a consequence of friction work and plastic flow can now be included in the computation of the tool temperature when forming Advanced High Strength Steel (AHSS) and Ultra High Strength Steel (UHSS); providing superior simulation accuracy. Looking beyond the sheet metal forming process PAMSTAMP provides for advanced checking of the final part shape on the control table and an assembly module that has been added to enable checking of tolerances of assemblies with stamped components.
Notably, ESI PAM-STAMP 2015 includes enhanced capabilities and new modules for CAD cleanup, piece cost estimation, nesting (to minimize raw material waste) and die surface design. These modules work seamlessly with ESI’s platform Visual-Environment and Dassault Systèmes’ CATIA V5 to provide a very complete and efficient solution for sheet metal forming engineering.
"ESI’s new and enhanced PAM-STAMP solution excels in speed, capability, accuracy and efficiency, from design/styling to try-out." - concludes Harald Porzner.
Image,video ©: ESI Group